Controlul cu ajutorul laboratorului de testare non-distructive
Metalwork Plant Apollo a fost mult timp de lucru cu compania „tehnologie“ care este „NON-distructiva LABORATOR“. Controlul lucrărilor efectuate pe teritoriul ZMK Apollo și dincolo.
Laboratorul efectuează controlul în domeniul securității industriale în industria prelucrătoare, construcții, și este independentă.
Laborator de certificare Certificare 1 Laborator 2 Laborator de acreditare de laborator de acreditare 1 2 3 Laborator Certificare de licență 1 licență de radiografie cu raze X 2 San epidem. Razele X 1 San epidem. Razele X 2
Ce metode sunt folosite?
Ce activități?
- încercări nedistructive în fabricarea, exploatarea, construcția, repararea, instalarea, reconstrucția și diagnoza tehnică a obiectelor de mai sus.
Care sunt obiectele de certificare?
- Structuri metalice (inclusiv: construcții din oțel de poduri)
Cine supraveghează?
- Controlul este efectuat de către persoane autorizate care au un „certificat de calificare“ și a recunoscut ca specialist de testare non-distructive.
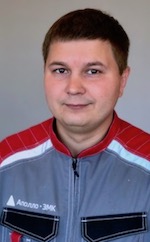
Șeful Laboratorului de testare non-distructive
Podmarov Sergey Aleksandrovich
Ce instrument este folosit?
- set VIC
- Detector cu ultrasunete defect A1212 «MASTER»
- Detector defect cu raze X
Cu ultrasunete detector de defect certificat A1212 MASTER de calibrare
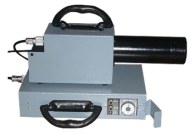
Care va fi rezultatul?
Conform rezultatelor de laborator emise prizonieri. care confirmă calitatea îmbinărilor sudate.
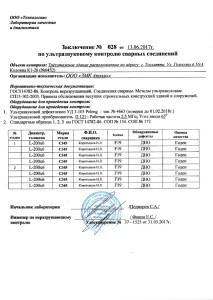
Încheierea UT
Această concluzie se aplică documentației, astfel cum a construit-a proiectului și confirmă calitatea produselor.
Această metodă este cea mai ieftină, mai rapidă și mai informativ. El este un distins și precede toate celelalte metode de testare non-distructive.
La examenul extern poate verifica calitatea pregătirii pentru asamblarea pieselor înainte de sudare, calitatea sudurii.
- identificarea urme de lovituri
- degajări
- huruit
- rugină
- urme de arsură
- sagging și alte defecte vizibile
puteți petrece un control vizual și măsurarea cu instrumente simple, dar, în ciuda simplității sale, necesită o abordare aprofundată. Acesta prevede dezvoltarea tehnologică harta, care stabilește metodele cele mai raționale și succesiunea de muncă.
Controlul VIC este reglementată de instrucțiunea din RD de control vizual și măsurarea 03-606-03. Care conține cerințele de calificare a personalului, înregistrează rezultatele, mijloacele de verificare, procesul de metode de monitorizare și evaluare.
într-un set standard include VIC
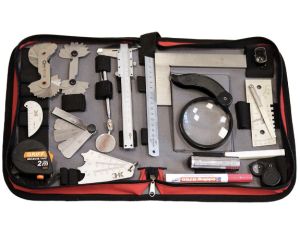
- șabloane sudor
- cot
- elipsograf
- lanternă
- marcator metalic
- lupă de măsurare
- cretă rezistent
- set sondă
- ruletă
- conducător
- oglindă cu un mâner
- rază și altele stabilite.
- Primul cec în alb înainte de asamblare. Ar trebui să existe nici o bavuri, ciupituri, scara, rugina, etc.
- Verificam calitatea canalului de sudură - marginile tocirea și colțul tăindu-le, pentru compușii cu Groove și T-articulațiilor.
- Măsurăm diferența dintre marginile la cap la cap și file de articulații, lățimea suprapunerii și decalajul dintre foile - pentru tur-articulare
- Colectate în cadrul piese de sudura cu abateri de la specificațiile tehnice sunt supuse corecției
- În continuare vom observa procesul de sudare. Monitoriza condițiile de sudare (tensiune, curent rata, hrana pentru animale), stabilitatea arcului, pentru executarea corectă a rolelor în cusături multistrat. Mai ales uita-te cu atenție la primul strat, folosind o lupă.
- În continuare, pentru a inspecta produsele finite. Ochiul liber sau cu o lupă pentru a detecta defecte articulațiilor - fisuri adâncituri, fistule, urme de arsuri, lipsa de fuziune. De asemenea, uita-te la forma cusătura - distribuție fulgi și distribuția globală de metal în amplificarea de sudură.
- Sudurile sunt comparate cu referință sau de a folosi modele speciale.
- Rezultatele măsurătorilor sunt înregistrate și trimite produsul înapoi pentru revizuire, dacă este necesar,
sudură suprafață exterioară caracteristică pentru fiecare sudură spo-soba, precum și poziția spațială, la un torus-sudare a fost efectuat. Uniformitatea fulg caracter zuet sudor de locuri de muncă, capacitatea sa de a menține o lungime constantă cu arc și viteza de sudare uniformă. Scales neuniformitate, lățime diferită și înălțimea punctului de sudură la fluctuația puterii arcului, rupturilor frecvente și instabilitatea arcului în timpul procesului de sudare. În această cusătură poate fi lipsa de penetrare, pori, zgură și alte defecte. La sudarea în poziții verticale sau homo mamare sudurile au o neuniformitate pronunțată fulgi hillocks șa și noduli. La sudarea în gaze protectoare în vid cordoanelor de suprafață exterioară netedă, lucioasă, fără solzi, și are formă de metal inventiv pătată-benzi.
Diagnosticul de suduri cu ultrasunete (UT) - este o metodă non-distructivă pentru integritatea controlului îmbinărilor sudate și caută defecte ascunse. USI este eficient atunci când caută goluri de aer, neomogenitatea compoziției chimice (includerea zgurii) și detectarea elementelor nemetalice.
Pentru prima dată, UT a avut loc în 1930 - nu este o metodă nouă. Dar este foarte popular și utilizat pe scară largă.
ultrasunetelor - urechea umană nu poate auzi, dar este baza pentru multe metode de diagnosticare. Multe industrii folosesc penetrare de diagnostic și de reflexie a sunetului. Mai ales în cazul în care nu este permis să facă rău unei persoane.
Mulți factori afectează calitatea UT:
- dispozitive de sensibilitate
- Configurare și calibrare defect
- alegerea unei metode mai adecvate, în funcție de experiența operatorului
Rosturile de (GOST 14782-86) și admiterea la operațiunea nu este posibilă fără eliminarea defectelor.
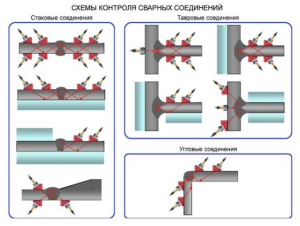
- por
- fisuri în zona afectată de căldură
- mănunchi metalice sudate
- lipsa de sudură penetrare
- din metal moale în partea inferioară a zonei de sudură
- svischeobraznogo defecte de caracter
- discontinuități și lipsa de cusătură de fuziune
- korozziey zona afectată
- O mulțime distorsiunilor geometrice dimensiune
- Loturi intruneasca compoziția chimică
Tehnologia se bazeaza pe abilitatea vysokochostytnyh oscilații pătrunde în metal și să se reflecte din golurile de suprafață, rugozitatea, coroziune și alte incluziuni în metalul de bază. Creează un val de sunet intră conexiunea în cazul defectului se abate de la distribuția normală. Acest lucru poate fi văzut pe dispozitiv și operatorul face o concluzie cu privire la detectarea defectelor. astfel încât să putem determina, de exemplu:
- dimensiunea relativă a defectului - amplitudinea impulsului reflectat
- distanța până vina - pentru timpul de propagare a undelor ultrasonice în metal
Procedeu de testare cu ultrasunete.
- În primul rând, vopseaua și rugina este îndepărtată în zona afectată de căldură fără Menne 100 mm pe fiecare latură
- Apoi, metalul în sine de suprafață și cusătură prelucrată vaselină sau glicerină, pentru un rezultat mai precis
- Am înființat instrumentul standard, în funcție de sarcina UT
- Verificați: grosime de până la 20 mm - setările standard (crestături) peste 20 mm - configurat graficul DGS.
- mișcări transversale longitudinale mutați traductorul (sonda) în raport cu sudură și a încercat să se rotească în jurul axei de la 10-150.
- După apariția sondei de semnal stabil este pivotat în zona de maximă amplitudine
- Dar uita-te la dacă nu este rezultatul reflecției din fluctuația cusătura (așa cum se întâmplă de multe ori)
- Dacă nu, repara defectul și scrie rezultatele
- Controlați parametrii în conformitate cu GOST
- Toate rezultatele sunt înregistrate în tabelul pentru a facilita găsirea și eliminarea defectelor
Conceput pentru a detecta defecte ascunse în îmbinări sudate.
Se bazează pe absorbția razelor X, în funcție de densitatea mediului și setul atomic de elemente care formează materialul mediului. Prezența defectelor duce la faptul că razele care trec prin metalul este atenuat în grade diferite. Iar observarea grinzilor ce se extind de distribuție de intensitate, se poate determina prezența și localizarea neomogenitatilor metalice.
- Împreună cu capacitatea de a identifica principalele defecte în suduri, putem vedea că nu prezintă nici o altă metodă - de exemplu, nepropai, scoici, și altele.
- Este posibil să se determine locația exactă a defectului detectat, permițând repararea rapidă
- rezultatele testului pot fi vizualizate pe film de raze X.
Aparatul este format dintr-un tub cu raze X într-o carcasă de protecție, generator de înaltă tensiune, și un cablu de control de la distanță. Unitatea de comandă este alcătuit dintr-un transformator, regulator de tensiune și dispozitive de măsurare de curent și a sistemelor de management de alarmă.
Generatorul de înaltă tensiune constă dintr-un transformator de filament tub, un redresor și transformator de înaltă tensiune.
Sursa de radiație (a aparatelor cu raze X) este selectat în funcție de grosimea metalului monitorizat și sensibilitatea necesară. Și pentru a obține o proiecție clară a sursei ar trebui să aibă o dimensiune mică și la fața locului focal situat la o distanță suficientă față de produs.
Dimensiunea minimă a defectului depinde de forma și locația.
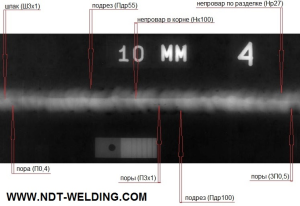
Cel mai bun dintre toate defectele identificate ale lungimii de-a lungul fasciculului de radiații penetrante. Astfel de imagini defecte sunt mai clare decât defectele curbate. Dar dacă defectul este la un unghi față de direcția de transiluminare, se deteriorează sensibilitatea și depinde de mărimea defectului și unghiul de deschidere între direcția radiografice și defect. Ca urmare a experimentelor a stabilit că defectele cu o mică deschidere (fisura) nu poate fi detectată dacă unghiul fasciculului de radiație în raport cu axa crăpăturii este mai mare de 7 grade.
Dimensiunile acceptate sunt precizate în desene și specificații. Dacă nu, ar trebui să fie ghidate de GOST 23055-78 „testare non-distructive. Sudarea metalelor topit. Clasificarea sudurilor pe rezultatele testelor radiografice. "